Un rooflet cobre no es de madera, así que lo que está haciendo en THISisCarpentry ? Bueno, trabajo con cobre requiere una gran cantidad de las habilidades que usamos todos los días de trabajo con la madera. En este proyecto, el rooflet tiene la intención de "mirar" como la madera, y sirve a un propósito que generalmente es ocupado por la madera. Claro, yo uso algunas habilidades que no son técnicamente consideradas "carpintería", pero si alguna vez has sudado el montaje de tuberías, o hecho una sartén intermitente de una puerta o ventana, o brilló un grillo, el valle, o la chimenea, que he conseguido las habilidades. Entonces, cepille conjunto de habilidades que con polvo, use su imaginación, y aplicarlo a un proyecto que podría estar gritando COBRE!
En primer lugar, algunos antecedentes sobre este proyecto. El cliente tiene gustos muy eclécticos, con un hogar de partidos y parece disfrutar de los detalles puntuales. Él ha hecho un toldo de lona, y la casa se detalla con el cobre de parpadear y canalones.
El propietario quería un pequeño techo para cubrir una puerta lateral de uso frecuente, pero no quería estar en una sombra. Esta puerta está en el lado norte de la casa, y ya está a la sombra de un roble bastante grande.
Me imaginé un techo de cobre con un panel de cristal que parecen "flotar" por encima de la puerta. Después de varios bocetos, que aterrizó en el diseño, que presenta al cliente. El cliente le gustó el diseño, y después de algún tiempo (nueve meses), decidió seguir adelante con el proyecto.
Ahora lo que necesitaba a la fuente el perfil y averiguar los detalles de la construcción. Mientras que los perfiles de cobre corona están disponibles, son caros (en más de $ 15 por pie de marcha), siempre un orden especial, y un perfil abierto. Mi plan consistía en el perfil para ser montado en superficie. Necesitaba una forma cerrada, así que lo que el perfil que tengo, yo tendría que crear esa forma cerrada por el boxeo en el perfil.
Después de los perfiles de abastecimiento, me di cuenta que podía lograr mi apariencia deseada utilizando cobre común, a nivel local de origen canaletas "K" de estilo. Por aquí corren $ 6 - $ 7 por pie lineal. Esto ayudaría a mantener los costos de material hacia abajo, y el precio final seguirá siendo atractivo para el cliente. 20 onzas. bobina de acero laminado en frío funcionado bien para las alcantarillas, y yo comúnmente disponibles de 20 oz intermitente de cualquier otra pieza que iba a necesitar en los perfiles visibles.
Desde mi diseño incluyó paneles de vidrio que añadir un peso considerable a la pieza-que prevé reforzar la estructura con un tubo interno "esqueleto" hecho de 1/2-in comúnmente disponibles. y 3/4-in. tipo "L" de tubos de cobre de fontanería y accesorios (ver foto, izquierda). Tipo "L" es aproximadamente el doble del grosor de tipo "M", que se utiliza para los sistemas de calefacción hidrónica. También decidió utilizar sin soldadura de plomo y el flujo de pasta fácilmente disponibles en cualquier ferretería o la salida de caja grande (lo que significaba que podría conseguir fácilmente más si me quedé sin). Los paneles de vidrio debía ser templado y laminado de seguridad y durabilidad, pero no pude especiales para el vidrio hasta que tuve la estructura principal montado para mediciones precisas.
Asamblea
Corté la población de canal (ver más abajo) usando mi mesa de la sierra con una hoja final. La hoja tenía un gancho de ángulo negativo, o al menos estaba cerca de cero, por lo que el cobre fue erosionado más que roto. Hice esto para eliminar las distorsiones, ya que el cobre, incluso en frío es más bien suave.
Me da la vuelta y revocó la corte de la pieza a utilizar en la realización de la "caja" del perfil de cierre (ver foto, derecha). No es un laminado de punta para el labio canal que quería reducir, pero no eliminar, porque pensé que se sumaría a la fuerza de la pieza terminada. I "aplastado" utilizando una cerradora mano de bloqueo-pinzas de tipo este me ha permitido "ajustar" la calabaza, lo que significa que fácilmente podría repetir el proceso para mantener la coherencia.
Yo inicialmente intentó utilizar un soldador comerciales para soldar las costuras, pero consideró que la "brecha de aire" en el labio obstaculizado la transferencia de calor. Me cambié a mi fiel y polvoriento Oxy / antorcha kit de acetileno, y se utiliza la soldadura o la punta de soldadura. Es importante destacar que el uso más amplio de la llama como se ve en una antorcha sudoración común para la plomería, se propaga el calor demasiado lejos y crea una gran distorsión. Si se puede soldar o soldar con Oxy / acetileno , usted no tendrá ningún problema con el control de velocidad y de las llamas. Decidí renunciar a la plancha, incluso en las zonas planas, porque me quería meter a un solo método, y no tener que cambiar constantemente de un lado a otro.
Reuní dos longitudes de tres metros del perfil, y luego cortarlas a la medida adecuada. Para este paso, he usado mi 12-en. SCMS, con el mismo tipo de hoja como la sierra de mesa. No puedo hacer suficiente hincapié en que hay que tomarse su tiempo y dejar que la herramienta haga el trabajo. Si usted va demasiado rápido que rasgar, rasgar, y distorsionar el perfil.
Reuní las piezas de una esquina a la vez, primero el esqueleto, entonces la corona sobre ella.
Me abrí camino a la vuelta pieza por esquina, con abrazaderas pony para mantener las cosas a tope apretado, cuidado de no aplicar demasiada presión mucho, para no deformar el cobre.
Los "esqueletos" salió hacia atrás a través del perfil para participar de las patas verticales de los soportes.
En la mayoría de lugares, que los soldados de refuerzo "esqueleto" a través y detrás de enclavamiento partes-esto ayuda a evitar puntos débiles. La columna central consistió en dos 1/2-in. tubos conectados a la estructura principal mediante remaches (ver foto, abajo), soldadura de múltiples capas juntas. Luego formó una caja de 20 onzas. cobre y soldados que con el perfil principal y la columna vertebral.
Cuando llegué a este punto, medida y ordenó a los paneles de vidrio. Me dijeron originalmente de tres semanas para la entrega, pero resultó ser seis semanas. Los paneles especiales todos los que pertenezcan a uno o dos proveedores nacionales, por lo que si tu chico de vidrio le da un plazo de ejecución, la figura sobre la duplicación de la misma.
Mientras esperaba el vidrio para llegar, he formado y aplicado los bordes de apoyo de vidrio. He añadido pop remaches de cobre hasta el "esqueleto" para mayor resistencia, como yo sabía que los paneles sería pesado.
Luego, volví mi atención a los soportes de apoyo. Al principio, he diseñado para puntales ligeramente curva, pero cuando he cargado algo de peso en el conjunto, se flexionan más de lo que quería. Si una rama fueron a caer sobre él, por ejemplo, simplemente se desplome hacia abajo, el bloqueo de la puerta se abra, y el perfil podría dividir abiertos.
Decidí utilizar un soporte más robusto hecho de 3/4-in recta. tubería reforzada con 1 / 2 pulgadas tubo interior. (Miré a usar varillas de acero inoxidable en el centro de fuerza, pero la disponibilidad y costes, a que un no-go).
Para aumentar la fuerza, integré la parte trasera intermitente y la caja en una sola. Esta pieza se deslizó sobre las piernas verticales para ser soldado y remachado a la zona oculta en la espalda, una capa de refuerzo de la otra.
En la espalda baja, el 1/2-in. tubo se inserta en la vertical de la pierna y soldadas. Entonces el 3/4-in. tubería, que se formó para adaptarse al contorno de superficie, fue soldado en su lugar.
Las patas verticales se formaron mediante la adopción de un 1/4-in. tubería de cobre, lo que hace un molde de madera, y la mano-formar en ellos una "D" de la sección transversal. Esto me dio una superficie plana contra la pared de la casa con una superficie visualmente redondeadas.
Para el molde de madera, hice una forma del bloque que tenía el contorno frontal de la pierna vertical que me permitió martillo la parte posterior plana, sin deformar gravemente la parte frontal redondeado, o dejar marcas, ya que sería la superficie que se vio.
El parpadeo se descolorida y distorsionado un poco, pero no me preocupa, porque eventualmente ser objeto de un herpes zóster de lucha contra el intermitente y el cedro.
La asamblea terminó parecía ser un objetivo en movimiento, constantemente me obliga a reevaluar mi enfoque y mantenerme en mi dedos de los pies. Mantener limpia también es importante. Limpie la pasta de flujo con una toalla caliente y húmedo a menudo, y limpie las manos, también.
Después de haber terminado el montaje, me lavé toda la pieza con agua caliente jabonosa y un estropajo de whisky de color rojo-brillante (disponible en los proveedores de carrocerías), para bajar toda la pasta de flujo residual y las decoloraciones. El whisky-brillante elimina cualquier resto de barniz del cobre, por lo que la pátina será aún. No se aplica un barniz ya que el cliente quería específicamente la pieza a la edad y pátina.
Instalación
Tomó cerca de tres horas para instalar el rooflet. Las molduras de corona alrededor de la puerta tenía que ser con muescas para permitir que las patas de soporte vertical para meter un poco detrás de él (ver foto, derecha). Esto hizo más fácil de instalar, ya que el rooflet se llevó a cabo en el lugar, lo que nos permitió liberar las manos en lugar de tener una persona constantemente la celebración de la pieza hasta que un tornillo se creó.
En primer lugar, elimina tres cursos de batidos (culebrilla) hasta el abrigo de la casa, que fue ... no existe. Hemos añadido butilo intermitente a la zona justo detrás y por encima de donde la rooflet iba a ser montado. Desde que fue un día de otoño frío, hemos tenido que grapar el butil intermitente en su lugar porque no se adhieren a la casa. Por supuesto, no tuvo problemas para pegarse a sí mismo!
Ed instalado algún relleno sacude superior, mientras que agregó que el acero inoxidable más bajos se queda a las patas de apoyo. A continuación añadimos el acabado sacude. Todos los parciales sacudidas por debajo de la rooflet fueron perforados para que no se rasguen durante el clavado en su lugar. A pesar de que fue preparado con el reemplazo de batidos, que al final no los necesitan. Tuvimos que retocar el tinte opaco. He añadido correspondiente movimiento de cargas detrás de los pernos de fijación inferior para evitar la deformación de la parte inferior de las patas de apoyo.
Después de la final de los retoques, el cliente-que había estado caminando de un lado una cuarta dentro de la casa, a escondidas y se asoma como un niño en Navidad, salió a ver el resultado final. No sólo era muy parecida a la ilustración del concepto que había conseguido casi un año antes (véase el principio del artículo), pero ahora podía apreciar plenamente la ligereza de los paneles de vidrio siempre. Después de preguntar por el tiempo que tomaría para que la pátina para iniciar el ajuste, yo le informó de que podría acelerar los plazos por el roce de un corte de limón o un trapo empapado de vinagre sobre la superficie. Su esposa quiere que se producen de forma natural, pero algo me dice que va a estar para arriba en una escalera dentro de un par de semanas, el limón en la mano.
Todo-en-todo, se trataba de un proyecto divertido, y he disfrutado de la libertad creativa que le permitió en hacer que suceda. Espero que esta historia inspira a algunos de ustedes que van más allá de su rutina habitual, utilice un conjunto de habilidades que ha acumulado algo de polvo, y pasar un buen rato!
Phil Herzegovitch es propietario de Dédalo Diseño LLC en Danbury, CT. Trabajando en su tercera y de tiempo completo carreras cuarta (contratista de remodelación y papá) que ha venido a darse cuenta de que la vida es una larga experiencia (es de esperar mucho tiempo de aprendizaje).
Después de salir de la escuela de ingeniería, Phil se convirtió en un maestro del Automóvil Técnico y un diseñador gráfico. Se metió con las profesiones, al mismo tiempo, hasta que perdió la pasión de ambos. Después de haber sido aprendiz de ebanista en la escuela secundaria, y un consejero de la madera en un campamento de verano, Phil todavía tenía un amor por la creación de las cosas que vio en su mente, y traducir esa visión en 3D con las manos. Así, después de un año la gestión de un taller de carrocería, decidió estacionar su caja de herramientas y artes de cambiar a la industria de la remodelación.
Como el diseño y construcción remodelador, Phil sigue recibiendo una emoción de la creación de una visión y traducirla en algo que va a durar muchos años. Todas sus experiencias pasadas contribuir a la capacidad de llegar a nuevas ideas para resolver muchos de los problemas que atraviesan en el sector de la construcción.
Cuando no está trabajando o completar elementos de la miel-enumera, Phil le gusta pasar tiempo con sus hijos, nadar con su hija, o la lucha libre (y persiguiendo a) sus muchachos niño gemelo.
Ver el artículo original (inglés)
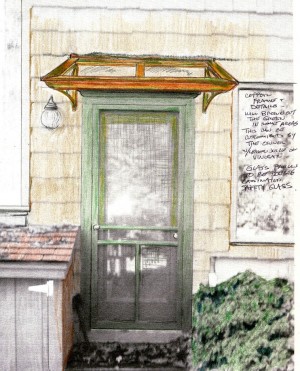
He creado esta ilustración utilizando una combinación de Adobe Photoshop, colorear a mano, y dibujando.
El propietario quería un pequeño techo para cubrir una puerta lateral de uso frecuente, pero no quería estar en una sombra. Esta puerta está en el lado norte de la casa, y ya está a la sombra de un roble bastante grande.
Me imaginé un techo de cobre con un panel de cristal que parecen "flotar" por encima de la puerta. Después de varios bocetos, que aterrizó en el diseño, que presenta al cliente. El cliente le gustó el diseño, y después de algún tiempo (nueve meses), decidió seguir adelante con el proyecto.
Ahora lo que necesitaba a la fuente el perfil y averiguar los detalles de la construcción. Mientras que los perfiles de cobre corona están disponibles, son caros (en más de $ 15 por pie de marcha), siempre un orden especial, y un perfil abierto. Mi plan consistía en el perfil para ser montado en superficie. Necesitaba una forma cerrada, así que lo que el perfil que tengo, yo tendría que crear esa forma cerrada por el boxeo en el perfil.
Después de los perfiles de abastecimiento, me di cuenta que podía lograr mi apariencia deseada utilizando cobre común, a nivel local de origen canaletas "K" de estilo. Por aquí corren $ 6 - $ 7 por pie lineal. Esto ayudaría a mantener los costos de material hacia abajo, y el precio final seguirá siendo atractivo para el cliente. 20 onzas. bobina de acero laminado en frío funcionado bien para las alcantarillas, y yo comúnmente disponibles de 20 oz intermitente de cualquier otra pieza que iba a necesitar en los perfiles visibles.
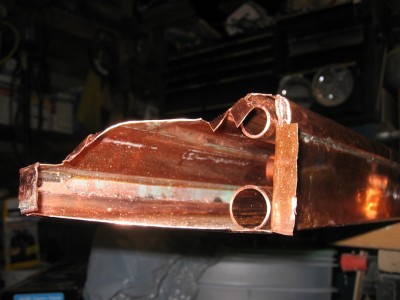
(Haga click en cualquier imagen para ampliar. Hit su navegador "Atrás" para regresar a este artículo.)
Asamblea
Corté la población de canal (ver más abajo) usando mi mesa de la sierra con una hoja final. La hoja tenía un gancho de ángulo negativo, o al menos estaba cerca de cero, por lo que el cobre fue erosionado más que roto. Hice esto para eliminar las distorsiones, ya que el cobre, incluso en frío es más bien suave.
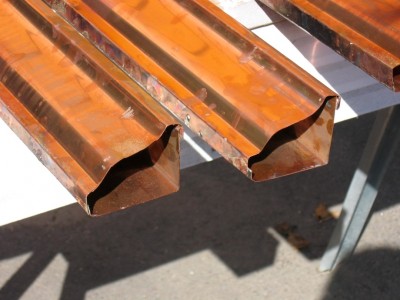
Yo inicialmente intentó utilizar un soldador comerciales para soldar las costuras, pero consideró que la "brecha de aire" en el labio obstaculizado la transferencia de calor. Me cambié a mi fiel y polvoriento Oxy / antorcha kit de acetileno, y se utiliza la soldadura o la punta de soldadura. Es importante destacar que el uso más amplio de la llama como se ve en una antorcha sudoración común para la plomería, se propaga el calor demasiado lejos y crea una gran distorsión. Si se puede soldar o soldar con Oxy / acetileno , usted no tendrá ningún problema con el control de velocidad y de las llamas. Decidí renunciar a la plancha, incluso en las zonas planas, porque me quería meter a un solo método, y no tener que cambiar constantemente de un lado a otro.
Reuní dos longitudes de tres metros del perfil, y luego cortarlas a la medida adecuada. Para este paso, he usado mi 12-en. SCMS, con el mismo tipo de hoja como la sierra de mesa. No puedo hacer suficiente hincapié en que hay que tomarse su tiempo y dejar que la herramienta haga el trabajo. Si usted va demasiado rápido que rasgar, rasgar, y distorsionar el perfil.
Los restos de piezas fueron cruciales para su instalación práctica. Desde el lado de perfil ondulado y aviones cambia mucho, tuve que cifra que se dobla ligeramente en forma y todavía me dan una superficie lo suficientemente grande para la soldadura a tomar. | ![]() |
El área plana era simple-me fui a él con una herramienta de rebordeado del automóvil , y golpeó las esquinas interiores con las costuras a mano. | ![]() |
Me abrí camino a la vuelta pieza por esquina, con abrazaderas pony para mantener las cosas a tope apretado, cuidado de no aplicar demasiada presión mucho, para no deformar el cobre.
Los "esqueletos" salió hacia atrás a través del perfil para participar de las patas verticales de los soportes.
![]() | ![]() |
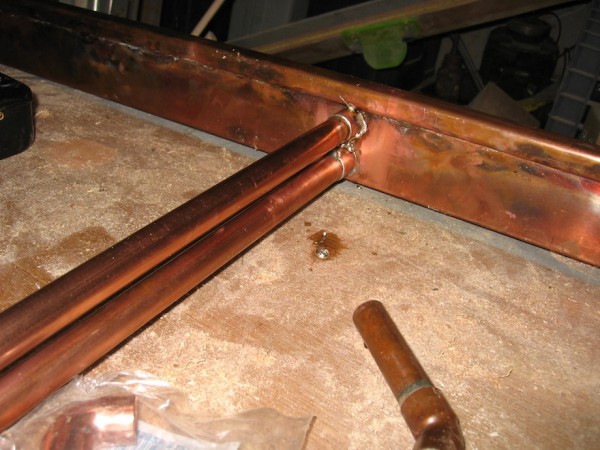
Centro de la columna vertebral, que consiste en dos 1/2-in. tubos conectados a la estructura principal mediante remaches
Mientras esperaba el vidrio para llegar, he formado y aplicado los bordes de apoyo de vidrio. He añadido pop remaches de cobre hasta el "esqueleto" para mayor resistencia, como yo sabía que los paneles sería pesado.
Luego, volví mi atención a los soportes de apoyo. Al principio, he diseñado para puntales ligeramente curva, pero cuando he cargado algo de peso en el conjunto, se flexionan más de lo que quería. Si una rama fueron a caer sobre él, por ejemplo, simplemente se desplome hacia abajo, el bloqueo de la puerta se abra, y el perfil podría dividir abiertos.
Decidí utilizar un soporte más robusto hecho de 3/4-in recta. tubería reforzada con 1 / 2 pulgadas tubo interior. (Miré a usar varillas de acero inoxidable en el centro de fuerza, pero la disponibilidad y costes, a que un no-go).
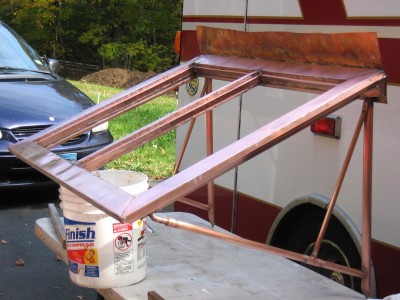
Para aumentar la fuerza, integré la parte trasera intermitente y la caja en una sola. Esta pieza se deslizó sobre las piernas verticales para ser soldado y remachado a la zona oculta en la espalda, una capa de refuerzo de la otra.
En la espalda baja, el 1/2-in. tubo se inserta en la vertical de la pierna y soldadas. Entonces el 3/4-in. tubería, que se formó para adaptarse al contorno de superficie, fue soldado en su lugar.
Las patas verticales se formaron mediante la adopción de un 1/4-in. tubería de cobre, lo que hace un molde de madera, y la mano-formar en ellos una "D" de la sección transversal. Esto me dio una superficie plana contra la pared de la casa con una superficie visualmente redondeadas.
Para el molde de madera, hice una forma del bloque que tenía el contorno frontal de la pierna vertical que me permitió martillo la parte posterior plana, sin deformar gravemente la parte frontal redondeado, o dejar marcas, ya que sería la superficie que se vio.
El parpadeo se descolorida y distorsionado un poco, pero no me preocupa, porque eventualmente ser objeto de un herpes zóster de lucha contra el intermitente y el cedro.
La asamblea terminó parecía ser un objetivo en movimiento, constantemente me obliga a reevaluar mi enfoque y mantenerme en mi dedos de los pies. Mantener limpia también es importante. Limpie la pasta de flujo con una toalla caliente y húmedo a menudo, y limpie las manos, también.
Después de haber terminado el montaje, me lavé toda la pieza con agua caliente jabonosa y un estropajo de whisky de color rojo-brillante (disponible en los proveedores de carrocerías), para bajar toda la pasta de flujo residual y las decoloraciones. El whisky-brillante elimina cualquier resto de barniz del cobre, por lo que la pátina será aún. No se aplica un barniz ya que el cliente quería específicamente la pieza a la edad y pátina.
Instalación
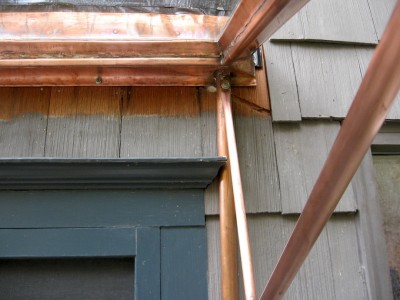
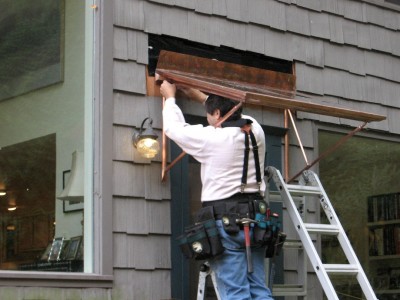
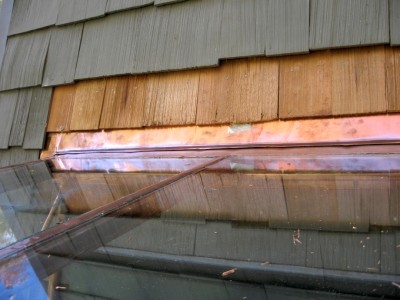
Ed instalado algún relleno sacude superior, mientras que agregó que el acero inoxidable más bajos se queda a las patas de apoyo. A continuación añadimos el acabado sacude. Todos los parciales sacudidas por debajo de la rooflet fueron perforados para que no se rasguen durante el clavado en su lugar. A pesar de que fue preparado con el reemplazo de batidos, que al final no los necesitan. Tuvimos que retocar el tinte opaco. He añadido correspondiente movimiento de cargas detrás de los pernos de fijación inferior para evitar la deformación de la parte inferior de las patas de apoyo.
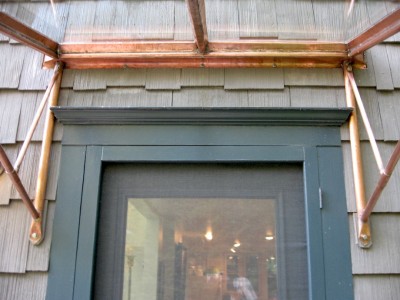
Todo-en-todo, se trataba de un proyecto divertido, y he disfrutado de la libertad creativa que le permitió en hacer que suceda. Espero que esta historia inspira a algunos de ustedes que van más allá de su rutina habitual, utilice un conjunto de habilidades que ha acumulado algo de polvo, y pasar un buen rato!
• • •
AUTOR BIO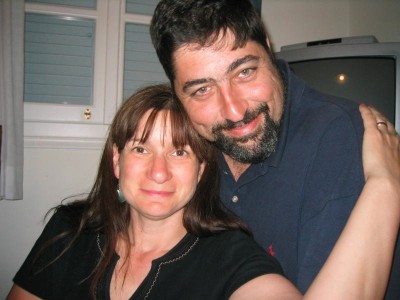
Phil Herzegovitch es propietario de Dédalo Diseño LLC en Danbury, CT. Trabajando en su tercera y de tiempo completo carreras cuarta (contratista de remodelación y papá) que ha venido a darse cuenta de que la vida es una larga experiencia (es de esperar mucho tiempo de aprendizaje).
Después de salir de la escuela de ingeniería, Phil se convirtió en un maestro del Automóvil Técnico y un diseñador gráfico. Se metió con las profesiones, al mismo tiempo, hasta que perdió la pasión de ambos. Después de haber sido aprendiz de ebanista en la escuela secundaria, y un consejero de la madera en un campamento de verano, Phil todavía tenía un amor por la creación de las cosas que vio en su mente, y traducir esa visión en 3D con las manos. Así, después de un año la gestión de un taller de carrocería, decidió estacionar su caja de herramientas y artes de cambiar a la industria de la remodelación.
Como el diseño y construcción remodelador, Phil sigue recibiendo una emoción de la creación de una visión y traducirla en algo que va a durar muchos años. Todas sus experiencias pasadas contribuir a la capacidad de llegar a nuevas ideas para resolver muchos de los problemas que atraviesan en el sector de la construcción.
Cuando no está trabajando o completar elementos de la miel-enumera, Phil le gusta pasar tiempo con sus hijos, nadar con su hija, o la lucha libre (y persiguiendo a) sus muchachos niño gemelo.
Ver el artículo original (inglés)
No hay comentarios :
Publicar un comentario